Revolutionize Your Manufacturing Process: Tips for Choosing the Best Cutting Tool
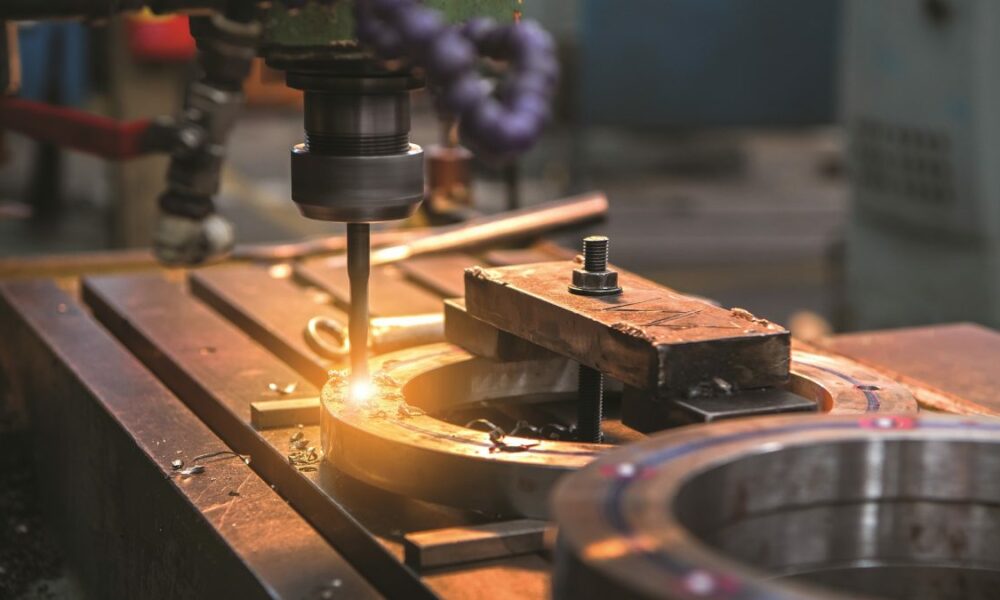
In the fast-paced manufacturing world, the tools you use can make or break your production process. Did you know that selecting the right cutting tool can increase manufacturing efficiency? The impact of using the correct tool is not just limited to speed; it also directly affects the quality of your products.
This article aims to provide you with essential tips for choosing the best cutting tool to optimize your manufacturing process, ensuring both efficiency and precision.
So, what’s the wait for? Let’s dig in!
Understand Your Manufacturing Needs
The first step in selecting the right cutting tool is understanding the materials you’ll be working with. Different materials, like metals, plastics, or composites, have unique properties that influence tool choice.
Precision is also crucial, especially when producing components with tight tolerances. For high-precision tasks, such as manufacturing aerospace components, investing in premium tools that offer superior accuracy is essential for optimal performance and product quality.
Evaluate Tool Material and Coatings
Cutting tools are made from various materials, each offering distinct advantages. Common options include carbide, high-speed steel (HSS), and ceramic. Carbide tools are prized for their durability and high cutting speeds, making them ideal for hard materials. HSS is more affordable and provides good toughness, making it suitable for general-purpose applications.
Ceramic tools are extremely hard and heat-resistant, perfect for high-speed tasks involving materials like cast iron. Coatings such as titanium nitride (TiN) or diamond further enhance these tools by increasing hardness, reducing friction, and extending tool life. This leads to more efficient cutting and reduced downtime, especially when working with hard materials.
Choose the Right Cutting Technique
Selecting the right cutting tool involves understanding different cutting techniques and their applications. For instance, plasma cutting and laser cutting are two popular methods today. Plasma cutting is highly effective for thick materials and offers fast cutting speeds, making it ideal for heavy-duty manufacturing tasks.
Laser cutting, on the other hand, provides exceptional precision and is perfect for intricate designs or thinner materials. When deciding between these techniques, it’s essential to consider the specific requirements of your project.
You might find it useful to compare laser cutting vs plasma cutting to understand the nuances of each method better. Depending on your needs, one may offer advantages that align more closely with your production goals.
Factor in Cost and Efficiency
Investing in high-quality cutting tools may require a higher initial cost, but they offer significant long-term savings. Durable tools reduce the need for frequent replacements and minimize downtime, leading to greater cost-effectiveness.
Better tools also enhance product quality, reducing rework and waste and boosting profitability. When evaluating tools, consider their lifespan—cheaper tools may wear out quickly, leading to higher long-term costs.
Tools made from advanced materials with protective coatings typically last longer, reducing replacement expenses. Additionally, efficient cutting tools consume less energy, lowering operational costs and supporting sustainability goals by making your manufacturing process more eco-friendly.
Prioritize Tool Maintenance and Support
Regular Maintenance
Maintaining your cutting tools, including sharpening and cleaning, is key to extending their life and ensuring consistent performance. Implementing a maintenance schedule and training staff on proper care can boost production efficiency.
Supplier Support
Choose a supplier with strong technical support, training, and replacement parts. They can assist with troubleshooting tool usage guidance and offer reconditioning services to restore tool performance.
Tool Reconditioning
Reconditioning tools are a cost-effective alternative to buying new ones, providing near-new performance at a fraction of the cost.
Test and Optimize Your Tool Selection
Trial Runs and Testing
Before fully integrating a new cutting tool into your production line, conducting trial runs is wise. Testing new tools in real-world conditions allows you to assess their performance and suitability for your specific application. This step helps you avoid costly mistakes and ensures the tools meet your manufacturing needs.
Collecting Feedback
Gather feedback from machine operators and production managers on the performance of new tools. Their hands-on experience can provide valuable insights into the tool’s effectiveness and any potential issues that may need addressing.
Continuous Improvement
The process of selecting the best cutting tool is ongoing. As production needs evolve and new technologies emerge, it’s important to evaluate and optimize your tool choices continuously. This approach ensures that your manufacturing process remains efficient and competitive.
Final Words
Selecting the right cutting tool is crucial for revolutionizing your manufacturing process. By understanding your needs, evaluating materials and coatings, considering cost and efficiency, prioritizing maintenance, and continuously optimizing your choices, you can significantly enhance your production quality and efficiency. Take the time to carefully assess your current tools and explore options for upgrading to more advanced technologies. With the right tools, your manufacturing process can achieve new levels of precision and productivity.