Unrevealing the Difference Between Spot Welding Machine and Butt Welding Machine
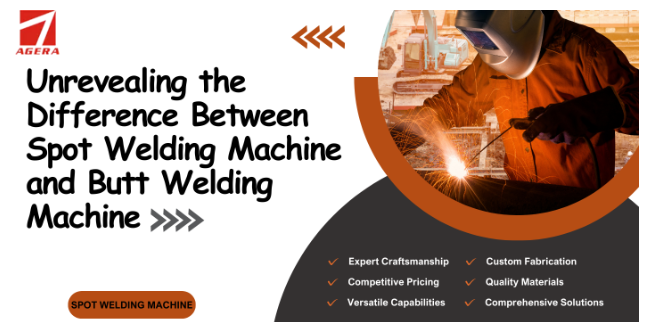
Welding is the backbone of many industries, serving as the essential process that joins materials together to create durable and long-lasting products. From the automotive industry to construction, the importance of welding cannot be overstated. But with so many different welding techniques and machines available, such as the Spot welding machine choosing the right one for your specific needs can be challenging. Two of the most commonly used welding methods are spot welding and butt welding. Each has its own set of advantages, applications, and unique characteristics.
What is Spot Welding?
Definition and Basic Principle
Spot welding is a type of resistance welding that joins two or more metal sheets together by applying heat and pressure to a small, localized area. This process is achieved by using electrodes that clamp the metal pieces together and then pass an electric current through the contact point, creating a weld.
Key Applications of Spot Welding
Spot welding is widely used in the automotive industry, particularly for assembling car bodies. It is also common in manufacturing household appliances, electronics, and other metal-based products that require quick and efficient joining of materials.
Advantages of Spot Welding
- Speed: Spot welding is incredibly fast, making it ideal for mass production.
- Automation: The process can be easily automated, reducing labor costs.
- Minimal Material Deformation: Spot welding causes minimal distortion, preserving the integrity of the materials being joined.
What is Butt Welding?
Definition and Basic Principle
Butt welding is a welding technique used to join two pieces of metal end-to-end. Unlike spot welding, which focuses on small, localized areas, butt welding creates a continuous weld along the entire length of the joint. This is typically done by heating the metal edges until they are molten and then pressing them together to form a solid bond.
Key Applications of Butt Welding
Butt welding is commonly used in the construction of pipelines, the manufacturing of metal structures, and the production of wire and cables. It is also used in various industrial applications where strong, seamless joints are required.
Advantages of Butt Welding
- Strong Joints: Butt welding produces joints that are as strong as the base materials.
- Versatility: It can be used on a wide range of metal types and thicknesses.
- No Filler Materials: Butt welding typically does not require additional filler materials, reducing costs.
Spot Welding vs. Butt Welding: Core Differences
Welding Techniques
Spot Welding Technique
Spot welding uses electrodes to apply pressure and heat to the exact spot where the weld is needed. The process is quick, and the welds are typically small, making it suitable for thin metal sheets.
Butt Welding Technique
In butt welding, the edges of the metal pieces are heated until they reach a molten state. The pieces are then pressed together to form a strong, continuous weld. This technique is ideal for creating long, seamless joints.
Material Compatibility
Materials Suitable for Spot Welding
Spot welding is most effective on thin sheets of metal, such as steel and aluminum. It is commonly used in applications where the materials are less than 3mm thick.
Materials Suitable for Butt Welding
Butt welding can be used on a wide variety of materials, including steel, aluminum, and copper. It is particularly useful for thicker materials and can join metals of varying thicknesses.
Strength of Weld
Comparing Weld Strength in Spot Welding
Spot welds are strong but localized, meaning the overall strength of the joint depends on the number of welds applied. They are sufficient for many applications but may not be ideal for heavy-duty uses.
Comparing Weld Strength in Butt Welding
Butt welding machine produces exceptionally strong joints, often as strong as the base materials themselves. This makes it suitable for structural applications where high strength is critical.
Cost Implications
Cost of Spot Welding
Spot welding is generally more cost-effective due to its speed and the minimal material required. It is an economical choice for mass production and high-volume projects.
Cost of Butt Welding
Butt welding can be more expensive, especially for large projects, as it requires more time and energy. However, the strong, seamless joints it produces can offset the higher initial cost.
Equipment Used
Overview of Spot Welding Equipment
Spot welding machines are relatively simple, consisting of a power source, electrodes, and a control unit. They are compact and can be integrated into automated systems.
Overview of Butt Welding Equipment
Butt welding machines are more complex, often requiring additional equipment for heating and pressing the metal pieces. These machines are typically larger and more expensive than spot welding machines.
Common Misconceptions about Spot and Butt Welding
Clarifying Common Myths
There are several misconceptions about spot and butt welding, such as the belief that spot welding is only for thin materials or that butt welding is always stronger. In reality, the effectiveness of each method depends on the specific application and materials used.
Practical Scenarios
For example, while spot welding is ideal for assembling thin metal sheets in automotive manufacturing, butt welding would be the preferred choice for constructing a high-pressure pipeline.
Choosing the Right Welding Technique for Your Needs
Factors to Consider
When choosing between spot welding and butt welding, consider factors such as the thickness of the materials, the required strength of the joint, and the overall cost of the project.
Industry-Specific Recommendations
For industries focused on mass production, such as automotive manufacturing, spot welding is often the best choice. On the other hand, industries that require strong, seamless joints, such as construction and pipeline manufacturing, may benefit more from butt welding.
Conclusion
Understanding the differences between spot welding and butt welding is crucial for selecting the right technique for your project. While spot welding offers speed and efficiency, butt welding provides strength and versatility. By considering the specific requirements of your application, you can choose the welding method that best meets your needs.
FAQs
What is the best welding technique for thin materials?
Spot welding is generally the best choice for thin materials, especially metal sheets less than 3mm thick.
Can spot welding be used on thick metals?
Spot welding is not typically used for thick metals, as it is most effective on thinner materials. Butt welding would be a better option for thicker metals.
How does the cost of equipment compare between spot welding and butt welding?
Spot welding equipment is generally more affordable and easier to maintain, while butt welding machines tend to be more expensive due to their complexity.
Is butt welding suitable for aluminum?
Yes, butt welding is suitable for aluminum, as well as a variety of other metals. It is especially useful for joining thicker aluminum pieces.
What industries primarily use spot welding?
Spot welding is primarily used in the automotive industry, as well as in the manufacturing of household appliances, electronics, and other metal-based products.
Read More From Techbullion And Businesnewswire.com